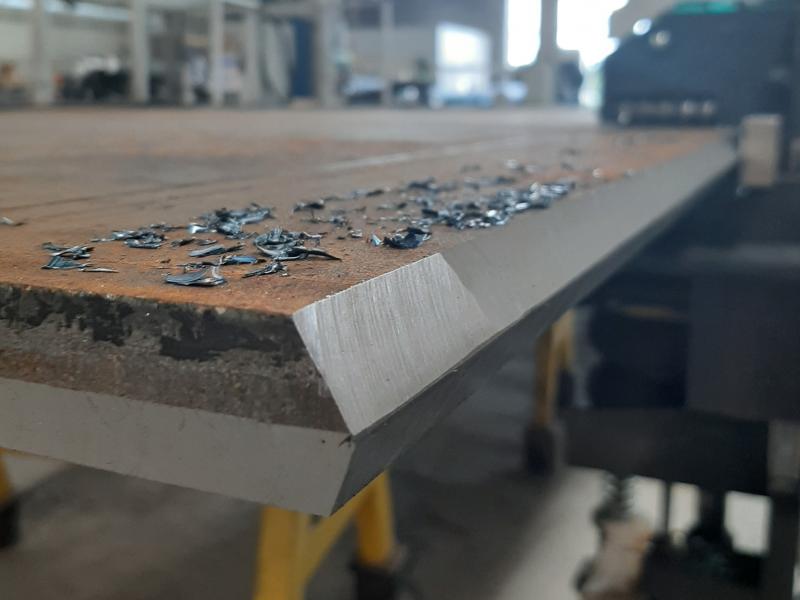
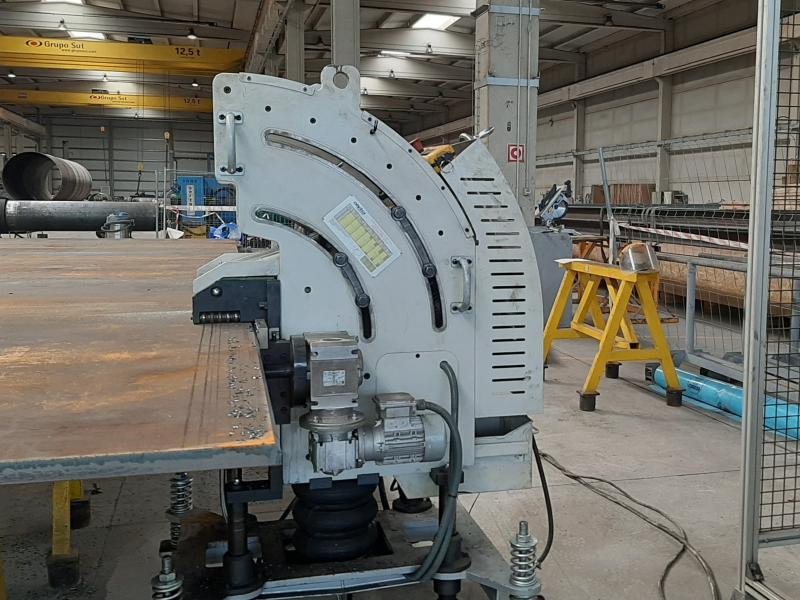
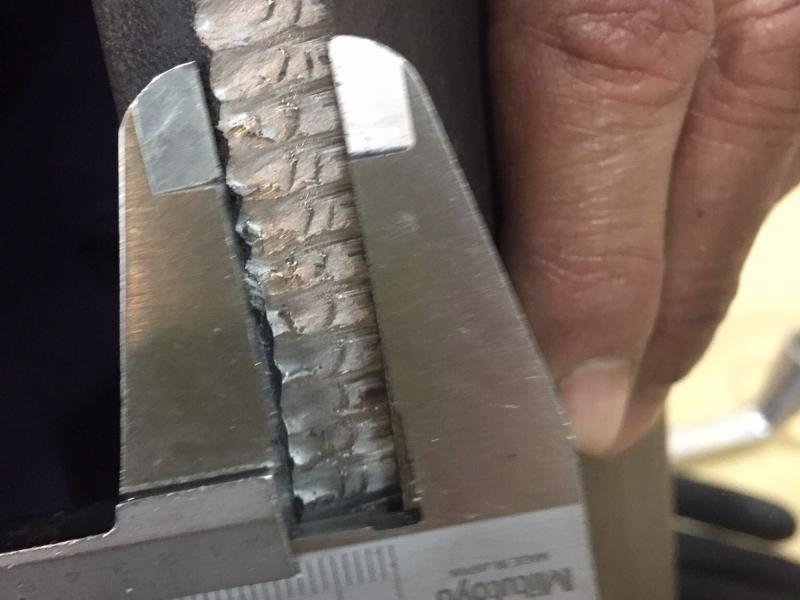

Laser-, Wasser- oder doch Plasmaschneiden? Eine investitionsaufwendige CNC-Anlage, die viel Platz in Anspruch nimmnt? Die mechanische Bearbeitung von Fasen ist in vielen Fällen ausgesprochen sinnvoll und findet bei vielen Anwendern Interesse und Beachtung. Nicht immer sind 3D-Konturfasen erforderlich. Viele Nutzer stehen häufig der Frage häufig gegenüber, welche Fasmethode für ihere Anwendung am wirtschaflichsten ist, da die Vorzüge des Fasvererfahrens je nach Anforderung und Werkstoff zur Geltung kommen. Doch stehen diese Verfahren in keiner Konkurrenz zueinander, sondern bilden bei vielen Fertigungsprozesses eine sinnvolle Allianz.
Folgend werden wir die gängigsten Verfahren zum Fasen erläutern.
• Mechanisches Anfasen
• Laserschneiden
• Wasserstrahlschneiden
• Plasmaschneiden
• Tabellarischer Überblick
Mechanisches Fasen mit Schweisskantenfräsen und Anfasmaschinen mit Rollenscheren
Neben den effizienten und professionellen Ergebnissen ist ein großer Vorteil der mechanisierten Schweißnahtvorbereitung die gesundheitsfreundliche Arbeitsweise. Im Gegensatz zu den gängigen Methoden zur Vorbereitung von Schweißnähten, bei denen Feinstäube oder sogar giftige Gase entstehen welche in die Umgebungsluft gelangen und so eingeatmet werden können, entstehen bei der mechanisierten Bearbeitung nur Fasenabschnitte, Frässpäne, Nibbelklumpen oder grobe Späne die einfach zu Boden oder in die dafür vorgesehenen Behälter fallen.
Damit für die bestmögliche Verbindungsgüte an der Schweißnaht gesorgt ist, müssen Öle, Fette, Lacke, Farben und Oxydschichten auf den Schweißteilen entfernt werden, so daβ die Stoßkanten an denen die Arbeiten ausgeführt werden metallisch rein sind. Auch sollte man bei der Bearbeitung auch dringend darauf achten, dass keine ölhaltigen Kühl- und Schmiermittel verwendet werden, um die Vorarbeit nicht wieder zu Nichte zu machen. Die mechanisierte Schweißnahtvorbereitung vermeidet genau dies. So verzichtet man bei dieser Vorgehensweise komplett auf emulsionshaltiges Kühlwasser, welches in den meisten Fällen bei der Schweißnahtvorbereitung mittels manuellen oder CNC-Fräsmaschinen zum Einsatz kommt und fräst, schert oder schleift das Material stattdessen komplett trocken.
Schweiβkantenfräsen
Mobile Fasenfräsmaschinen lösen die klassischen Verfahren zur Schweißnahtvorbereitung, wie Rollenscheren, Brennen und manuell mittels Winkelschleifern immer mehr ab. Moderne, leistungsfähige Maschinen sorgen nicht nur für mehr Effizienz, sondern überzeugen auch durch die hohe Oberflächenqualität. Die Maschine fährt zum Blech, daher ist ihr Einsatz sehr flexibel.
Mobile Fasenfräsmaschinen zeigen gerade beim Einsatz bei großen Blechdicken ihr Können. Mit Rädern ausgestattet fahren diese Maschinen bei Bedarf selbstständig an der geraden Blechkante entlang. Für Oberfasen und Unterfasen kann auf verschiedene Modelle zurückgegriffen werden und macht somit ein aufwendiges Plattenwenden unnötig.
Kantenbearbeitung mit dem Scherverfahren
Die effizienteste Möglichkeit der Schweißnahtvorbereitung sind die Rollenscherenmaschinen.
Diese Fasen-Schermaschinen arbeiten nach dem Rollenscherenverfahren. Hierbei wird ein langer Span von der Blechkante mittels eines langsam drehenden Schneidrades bzw. Scherrad abgeschert. Hierdurch werden Geschwindigkeiten von bis zu 3 m/min (bis zu 5 mal schneller als herkömmliche Verfahren) erreicht. Die Kosten für den Meter Fase fallen bis zu 75% geringer aus als bei anderen Verfahren! Ohne Staub und ohne Lärm, da keine Frässpäne und kein Schleifstaub entsteht. Eine sehr effiziente und wirtschaftliche Methode zur Schweißnahtvorbereitung. Langlebige Schneidräder sind für Stahl und Edelstahl bestens geeignet.
Vor- und Nachteile
Die Vorteile
- Schneiden aller leitfähigen Werkstoffe
- Schneiddicken bis zu 100 mm
- Schneiden hochlegierter Stähle
- Geräuscharm
- Hohe Wirtschaftlichkeit
- Optimale Materialausnutzung
- Geringe Schnittfugenbreite
- Keine thermische Belastung
- Schneiden dicker Materialstärken
- Sicherer für Anwender und die Umwelt
- Keine Nachbearbeitung erforderlich
- Geringe Betriebskosten
- Hohe Schnittgeschwindigkeit
- Geringe Set-up-zeiten
- Kein spezialisiertes Personal notwendig
- Ohne grössen Beschränkung der Teile.
Nachteile
- Rauhes Endergebis bei Rollenscheren.
- Hohe Spezialisierung, nicht für andere Verfahren anwendbar.
- Begrenzte Materialstärken
Merkmale des Lasers
Der Laser hat auf dem Gebiet der Blechbearbeitung neue Anwendungen erschlossen. Gerade im Dünnblechbereich führt aufgrund der hohen Schnittgeschwindigkeiten und geringen thermischen Belastung am Laserschneiden kein Weg vorbei. Dabei besticht die Laserbearbeitung durch nahezu rechtwinkligen Schnittkanten und einem minimalen Schnittspalt mit erzielbaren Toleranzen bis +/- 0.1 mm/m. Auch eine schier unbegrenzte Materialvielfalt haben den Laser in vielen Bereichen zur Nummer 1. unter den Schneidwerkzeugen werden lassen. So können Edelstahl bis 50 mm, Stahl bis 40 mm und Aluminium bis 20 mm sicher geschnitten werden. Aber auch bei anderen Werkstoffgruppen wie Holz, Kunststoff oder auch Papier kommen Laser für die Bearbeitung zur Anwendung. Nachteilig wirken sich beim Laserschneiden die verminderte Prozessstabilität bei spiegelnden Oberflächen, ein begrenzter Blechdickenbereich und die umfangreiche Arbeitsschutzmaßnahmen aus.
Vor- und Nachteile
Vorteile
- Hohe Schnittgeschwindigkeiten
- Optimale Gratfreiheit
- Geringer Wärmeeinfluss
- Perfekte Maßgenauigkeiten
- Beste Materialausnutzung
- Kurze Bearbeitungszeiten
- Minimaler Schnittspalt
- Große Materialvielfalt
Nachteile
- Hohe Investitionskosten
- Begrenzte Materialstärken
- Umfangreicher Arbeitsschutz
- Prozessinstabilität bei Spiegelungen
Schneiden mit dem Wasserstrahl
Wasserstrahlschneiden ist eine effektive Alternative zu den konventionellen Trennverfahren und für viele Anwender die optimale Schneidlösung. Vom Schaumstoff bis zum harten Saphir, mit einem Hochdruckwasserstrahl von bis zu 6.200 bar werden auch die härtesten Werkstoffe weich wie Butter. Bei hitzeempfindlichen Materialien ist dieses kalt Schneidverfahren eine gute Lösung. Durch neueste technologische Entwicklungen stößt dieses innovative Verfahren in neue Genauigkeits- und Produktivitätsbereiche vor. Das Ergebnis ist eine wesentliche verbesserte Qualität der Teiletoleranz und Winkelgenauigkeit. Durch Beimischung scharkantiger Abrasive wie Sand oder Quarz kann die Wirkungsweise des Wasserstrahlschneidens nochmals gesteigert werden, weshalb auch sehr dicke Materialstärken geschnitten werden können. So lassen sich Edelstahl bis 300 mm und Aluminium bis zu einer Dicke von 400 mm schneiden.
Vor- und Nachteile
Die Vorteile
- Hohe Wirtschaftlichkeit
- Große Materialvielfalt
- Optimale Materialausnutzung
- Geringe Schnittfugenbreite
- Keine thermische Belastung
- Schneiden dicker Materialstärken
- Hohe Präzision bis in den Mikrobereich
- Sicherer für Anwender und die Umwelt
- Oft keine Nachbearbeitung erforderlich
Nachteile
- Hohe Betriebskosten
- Große Korrosionsgefahr
- Langsame Schnittgeschwindigkeit
- Aufbereitung des Schneidwassers
- Entsorgung der Abrasive
Erklärungen zum Plasmaschneiden
Plasmaschneiden hat in den letzten Jahren aufgrund der Entwicklung modernster Mehrgasbrenner deutliche Fortschritte gemacht und zählt gerade bei dicken CrNi-Blechen sowie im mittleren Stahlbereich zu den wirtschaftlichsten Trennverfahren. Dabei gleicht die Schnittqualität im Dickenbereich von 15 mm bis 40 mm der des Laserschneidens. Doch besticht dieses thermische Trennverfahren mit hohen Schnittgeschwindigkeiten, weshalb die Produktivität des Fertigungsprozesses deutlich gesteigert wird. Gerade bei der Fertigung von Bauteilen, welche in der weiteren Bearbeitung noch geschweißt, gedreht, gefräst oder weiter mechanisch bearbeitet werden müssen, bietet das Plasmaschneiden umfangreiche Vorteile.
Vor- und Nachteile
Die Vorteile
- Schneiden aller leitfähigen Werkstoffe
- Schneiddicken bis zu 200 mm
- Hohe Qualität in mittleren Stärken
- Schneiden hochlegierter Stähle
Nachteile
- Hohe Betriebskosten
- Relativ breiter Schnittspalt
- Meist großer Lärmpegel
- Aufhärtung der Randzonen
- Nachbearbeitung erforderlich
Fazit zum Vergleich
Was ist das beste Schneidverfahren?
Darauf gibt es keine eindeutige Antwort, denn zunächst gilt es zu klären, was man unter dem Begriff des "Besten" versteht? Und je nach Schneidaufgabe eignet sich ein bestimmtes Verfahren am sinnvollsten. Kein Verfahren kann als einzig Richtiges angesetzt werden, sondern alle Schneidverfahren haben ihre Berechtigungen, ihre speziellen Einsatzgebiete, Stärken und Schwächen, Vor- und Nachteile und individuelle Kostenstrukturen.
Es kommt immer auf den Einsatzfall an.
Was sind Ihre Kriterien für einen guten Zuschnitt, für den besten Schnitt?
Sind es die Herstellkosten des Zuschnitts?
Ist es die Genauigkeit gemäß der ISO 9013 der Zuschnittteile?
Ist es der thermische Einfluss, die Gefügeveränderung im Material?
Ist es die Schweißbarkeit der Zuschnitte?
Ist es die Aufhärtung des Materials und damit der Tauglichkeit für die ISO 1090 Execution Classes?
Erfordert die Materialgüte bestimmte Behandlungsregeln?
Ist die Geometrieanforderung an den Zuschnitt sehr hoch?
Wie sieht die Nachbehandlungen des Zuschnitts aus, soll lackiert, Pulver beschichtet oder verzinkt werden?
etc.
Die Vielzahl der Kriterien macht daher pauschale Aussagen unmöglich. Erheblich ist die Anforderung Ihres Kunden und die Wirtschaftlichkeit der Fasenerstellung.
Laserschneiden ist gerade im Dünnblechbereich stets die erste Wahl und besticht mit einer hohen Wirtschaftlichkeit. So können Werkstücke aus den unterschiedlichsten Werkstoffgruppen, ohne mechanische Nachbearbeitung mit einer sehr hohen Bauteilegenauigkeit gefertigt werden.
Bei Materialstärken über 300 mm kommen nur der Brenner und das Wasserstrahlschneiden in Frage. Mit einem Blick auf die Qualität ist sicherlich eine Entscheidung zum Wasserstahlschneiden logisch, aber nicht alle Anwender können diese Investition tätigen und haben auch nicht den notwendigen platz hierzu.
Geht nur darum, den Anfasprozess zu rentabilisieren liegt die Entscheidung zum mechanischen Fasprozess nahe. Gesundheitsschonend, witschaftlich und handlich sind die mechanischen Verfahren. Von Blechstärken von 3mm bis 100 mm können hier verschiedene Lösungen geboten werden. Dabei ist die Endverarbeitung sehr unterschiedlich. Bei Anfasmaschinen mit Rollenscheren entstehende Fase ist bezüglich der Winkelgenauigkeit sehr präzise, hat aber eine raue Oberfläche, welche durch die Einwirkung des Schneidrades entsteht. Dieses Riffelmuster spielt jedoch für den darauffolgenden Schweißprozess keine Rolle, da das Material beim Schweißen komplett aufgeschmolzen wird.
Ist die Endverarbeitungsanforderung hoch sind die Schweisskantenfräse eine sehr gute Alternative. Auch sehr wiederstandsfähige Metalle wie Hardox und Duplex können bearbeitet werden und Fasen bis zu 60mm erstellt werden.
Der grosse Nachteil der Anfasmaschinen liegt vor allem in ihrem hohen Grad ihrer Spezialisierung, sie können nichts anderes.