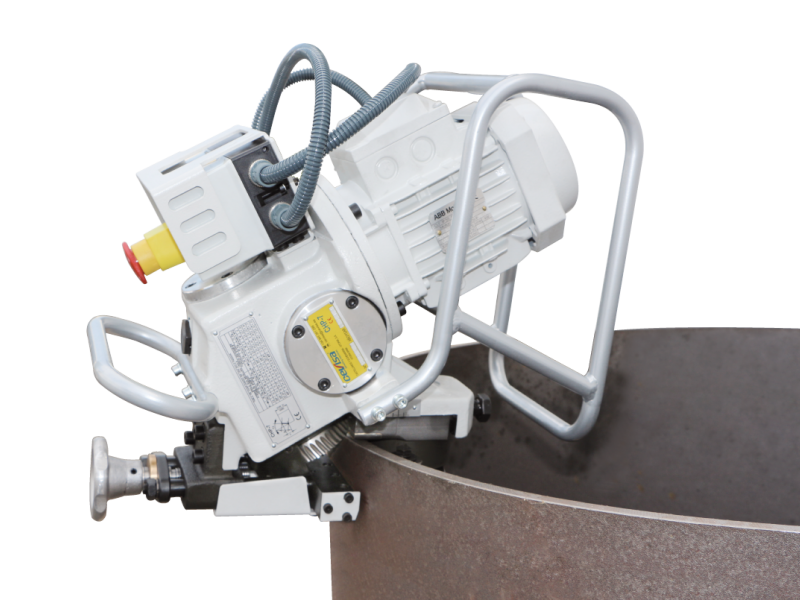
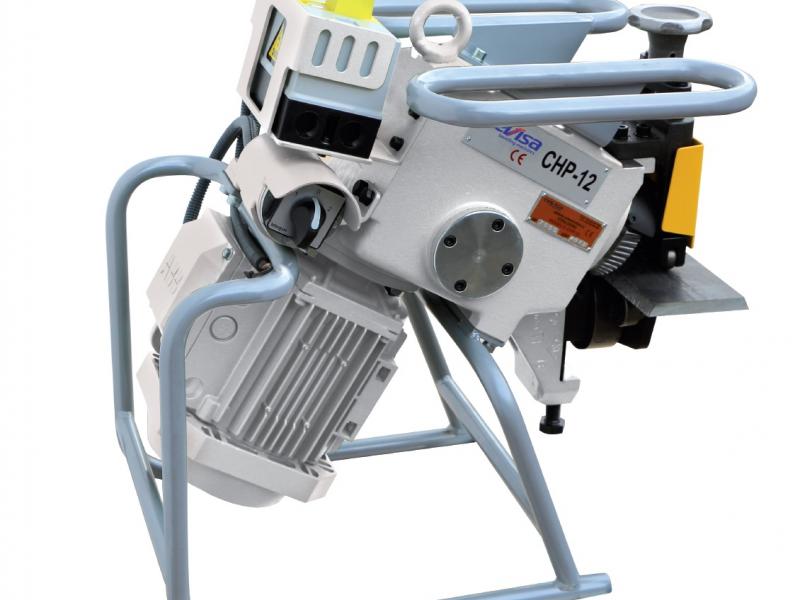
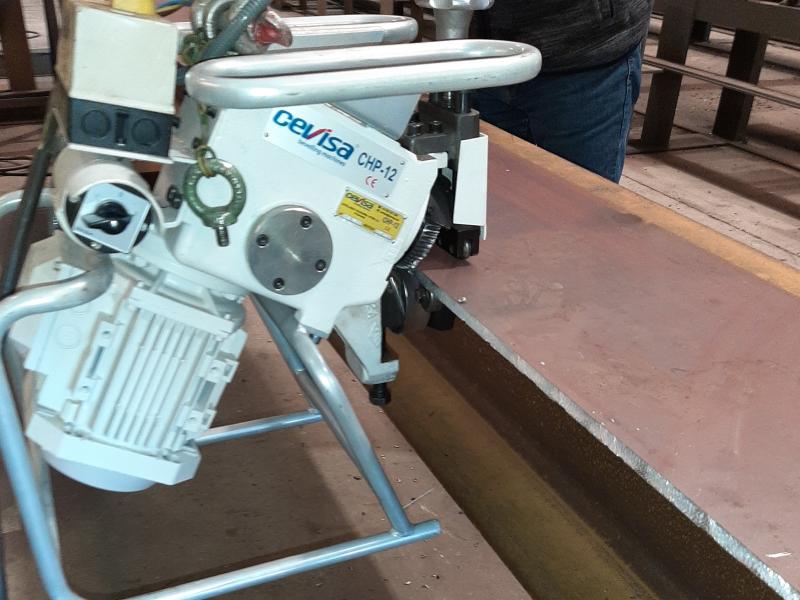
In Metall-Fertigungsbetrieben ist das Anfasen häufig einer der relevanten Prozesse, denen nicht die angemessene Bedeutung zukommengelassen wird. Zweifellos ist eine schlechte Schweißkantenvorbereitung die erste und grundlegendste Ursache für unsachgemäße Einstellungen, die zu Schweißnähten schlechter Qualität aufgrund ungenauer V-Verbindungsvorbereitungen führen. Ein übermäßiges Schweißen, erhöhterWärmeeintrag und erhöhter Aufwand von Verbrauchsmaterialien und Personal sowie zusätzliche Stunden sind die Folgen. All diese Faktoren tragen zu einer geringeren Produktivität bei zusätzlichen Kosten bei, die den heutigen Anforderungen an eine Kostenoptimierung schaden.
Die Bedeutung einer genauen Schweißnahtvorbereitung ist gut nachzuvollziehen, wenn man ein paar Sektoren der Schwerindustrie genauer betrachtet, wie z.B. den Schiffbau oder die Herstellung von Rohrtürmen der Windenergie.
Die Herstellung von Windmühlen-Röhrentürmen ist nicht so komplex wie der Schiffbau, ist allerdings auf das Schweissen einer großen Anzahl von Blechen mit konstanter Präzision angewiesen, um die Schale zu produzieren, die den Turm von bis zu 100 m bilden. Diese spezielle Anwendung erfordert Fasen von mindestens 1500 m an einem Tag (drei Schichten) für ein Produktionsniveau von "ein Turm pro Tag". Bei beiden oben genannten Sektoren besteht die Notwendigkeit einen schnellen, präzisen, konsistenten und wirtschaftlichen Fasprozess mit minimalem oder keinem Wärmeeintrag zu finden, um Schweißnähte guter Qualität für Kohlenstoffstähle, hochfeste Stähle, rostfreie Stähle, Aluminium und andere legierte Stähle zu ermöglichen.
Prozessauswahl: Die Auswahl des am besten geeigneten Prozesses kann komplex sein, da viele Faktoren berücksichtigt werden müssen. Möglicherweise gibt es nur wenige Optionen, die für eine bestimmte Anwendung geeignet sind. Die endgültige Wahl hängt jedoch im Allgemeinen von der Fähigkeit ab, die erforderlichen Qualitätsblenden wirtschaftlich herzustellen. Diese Faktoren können umfassen:
• Art des Materials.
• Bereich der abzuschrägenden Blechstärken.
• Erforderliche Schnittqualität.
• Komplexität der Kantenvorbereitung.
• Präzision des Schneidprozesses.
• Anzahl der Bleche / Rohre
• Zulässige Toleranzen des Prozesses.
Am meisten wird das Verfahren des Autogenschneidens (Anfasen) zum Schneiden von Kohlenstoffstahlplatten verwendet. Manuelle Geräte sind kostengünstig und können manuell verwendet werden.
Nachteile der Verwendung dieses Verfahrens können niedrige Geschwindigkeiten, hoher Wärmeeintrag, mögliche Ungenauigkeiten in den Fasenwinkeln und Fasoberfläche (was zu übermäßiger Schweißnahtablagerung führt) sein. Darüber hinaus entstehen erhebliche Kosten für Gase und andere Verbrauchsmaterialien, einschließlich der unvermeidlichen Abfälle und Arbeitskräfte. Wenn CNC-Flammenschneidemaschinen verwendet werden, müssen die Platten in die Maschine eingespeist werden, und dies impliziert die Verwendung eines Krans, was eine kostspielige und zeitaufwändige Operation ist, und wir würden nicht länger von Geräten mit geringen Investitionen sprechen.
Im Gegenzug verfügt CEVISA über Fasenmaschinen, die unter anderem nach dem Rotationsscherprinzip arbeiten und aufgrund ihrer Tragbarkeit und Manövrierfähigkeit bei hoher Fasgeschwindigkeit von 1,7 bis 2,6 m pro Minute sehr effektiv sind. Diese Schweisskantenformer können Platten mit einer Dicke von 6 bis 50 mm anfasen und bieten präzise und gleichmäßige Schweissnahtvorbereitung „V“, „K“ oder „X“. Mit diesen Maschinen können verschiedene Werkstoffe wie Kohlenstoffstähle, legierte Stähle, rostfreie Stähle, Aluminium sehr erfolgreich gefast werden. Das mechanische Fasen, bei dem es sich nicht um einen thermischen Prozess handelt, hat den wichtigen metallurgischen Vorteil, dass keine wärmemodifizierte Zone erzeugt wird und keine thermischen Verzerrungen verursacht werden.
Weitere bedeutsame Vorteile des mechanischen Fasens sind:
1. Betrieb frei von Lärm, Verschmutzung und Vibrationen.
2. Diese Maschinen können leicht zur Arbeit getragen werden und sind selbstfahrend und folgen der Kante der Platte, während sie ohne Unterstützung des Bedieners gefast werden.
3. Der gefederte Wagen ermöglicht den Betrieb der Maschine auf unebenem Boden.
4. Schnelle und einfache Einstellung.
6. Für die Bedienung dieser Maschinen sind keine besonderen Fähigkeiten erforderlich.
7. Die Ober- und Unterseite der Platten kann gleichzeitig mit zwei Maschinen gefast werden.
Invertierte oder drehbare Fasenmaschinen, die gleichzeitig in Verbindung mit Standard-Fasenmaschinen verwendet werden, können eine Doppel-V-Fase erzeugen, ohne die Bleche zu drehen. Dies spart Kranzeit, Bearbeitungszeit und Wiederholungszeit, komprimiert die Gesamtdurchsatzzykluszeit und erhöht sich Produktivität zu optimierten Kosten.
All diese Faktoren machen Fasenmaschinen zweifellos zu einer bevorzugten Wahl in der Fertigungsindustrie, um die Schweißnahtvorbereitung und die Schweißqualität in der Basis zu verbessern und hohe Schweißkosten zu vermeiden. Gute Schweißer sind teuer und knapp, und darum ist es konsequent zu erkennen, dass Konsistenz in Qualität und Ästhetik ebenfalls von größter Bedeutung sind.